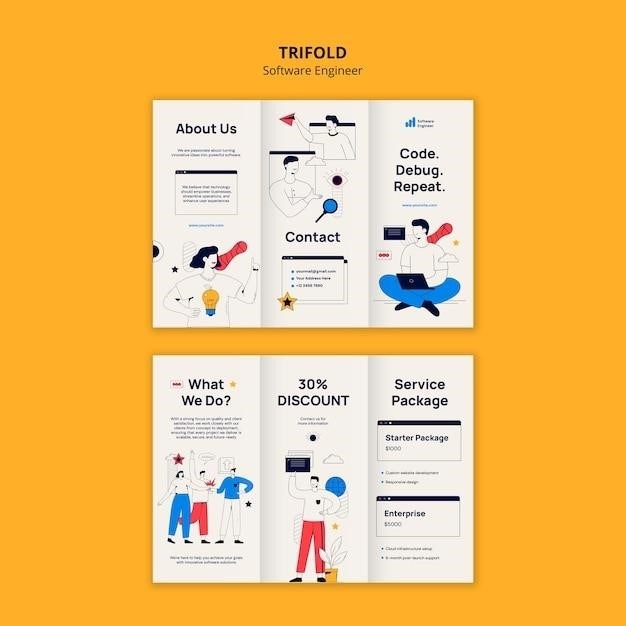
Manual Handling Risk Assessment⁚ A Comprehensive Guide
This guide provides a comprehensive overview of manual handling risk assessments‚ covering their purpose‚ legal requirements‚ steps involved‚ examples‚ resources‚ and templates. It delves into identifying hazardous tasks‚ assessing risk factors‚ evaluating risks‚ and implementing control measures. Additionally‚ it explores the use of assessment checklists and the importance of considering individual factors in the assessment process.
Introduction
Manual handling‚ encompassing tasks like lifting‚ carrying‚ pushing‚ pulling‚ and restraining objects‚ is a common activity across various workplaces. While seemingly straightforward‚ these tasks pose significant risks to individuals’ health and safety‚ potentially leading to musculoskeletal injuries‚ particularly in the back‚ neck‚ and shoulders. These injuries can result in pain‚ discomfort‚ reduced mobility‚ and even long-term disability‚ impacting individual well-being and workplace productivity. Recognizing these inherent risks‚ a robust manual handling risk assessment process is essential for organizations to proactively identify‚ evaluate‚ and control hazards associated with these tasks. This guide aims to provide a comprehensive framework for conducting effective manual handling risk assessments‚ enabling workplaces to minimize the risk of injury and create a safer working environment for all.
Why Conduct a Manual Handling Risk Assessment?
Conducting a thorough manual handling risk assessment is crucial for several compelling reasons. Firstly‚ it serves as a proactive measure to identify and address potential hazards before they result in injuries. By systematically analyzing tasks and identifying risk factors‚ organizations can implement appropriate control measures‚ reducing the likelihood of accidents and ensuring a safer working environment. Secondly‚ it demonstrates a commitment to worker safety and well-being‚ fulfilling legal obligations and promoting a positive workplace culture. Thirdly‚ it can significantly reduce the financial burden associated with workplace injuries. By preventing accidents‚ organizations can avoid the costs of medical treatment‚ lost workdays‚ insurance claims‚ and potential legal liabilities. Lastly‚ a well-conducted risk assessment fosters a culture of safety awareness among employees‚ empowering them to identify risks‚ report concerns‚ and participate in creating a safer workplace. In summary‚ conducting a manual handling risk assessment is not just a legal requirement but a responsible and strategic decision that benefits both individuals and organizations.
Legal Requirements
The legal framework surrounding manual handling risk assessments is designed to protect workers from the risks associated with hazardous manual handling tasks. The Manual Handling Operations Regulations 1992 (as amended) in the UK‚ for instance‚ places a legal obligation on employers to take reasonable steps to avoid hazardous manual handling tasks. If these tasks cannot be avoided‚ employers must assess the risks involved and implement control measures to minimize the risk of injury. These regulations emphasize the importance of considering the load‚ the individual‚ the task itself‚ and the environment in which the task is performed. Failing to comply with these regulations can result in legal consequences‚ including fines and prosecution. Moreover‚ organizations must ensure their employees are adequately trained in recognizing and addressing manual handling risks. This training should cover identifying hazardous tasks‚ understanding risk factors‚ and implementing safe handling techniques. By adhering to these legal requirements‚ organizations create a safer working environment‚ demonstrate a commitment to worker safety‚ and protect themselves from legal liabilities.
Steps Involved in a Manual Handling Risk Assessment
A comprehensive manual handling risk assessment involves a structured process to identify‚ evaluate‚ and control risks associated with manual handling tasks. This process typically includes the following steps⁚
- Identify Hazardous Manual Handling Tasks⁚ This initial step involves identifying all tasks within the workplace that involve manual handling‚ such as lifting‚ lowering‚ pushing‚ pulling‚ carrying‚ or restraining objects. The assessment should consider all potential hazards‚ including those that might not be immediately obvious.
- Assess Risk Factors⁚ Once hazardous tasks are identified‚ the next step is to assess the risk factors associated with each task. This involves considering the load being handled (its weight‚ size‚ shape‚ and stability)‚ the individual performing the task (their physical capabilities and training)‚ the task itself (including frequency‚ duration‚ and posture)‚ and the environment (lighting‚ space‚ and potential obstacles).
- Evaluate the Risk⁚ After identifying and assessing risk factors‚ the next step is to evaluate the overall risk associated with each task. This involves considering the likelihood of an injury occurring and the severity of that injury. This evaluation helps prioritize tasks based on their risk levels‚ focusing on those posing the greatest potential for harm.
- Control Measures⁚ The final step involves implementing control measures to eliminate or reduce the risks identified in the assessment. This can involve eliminating the task altogether‚ substituting it with a safer alternative‚ or implementing engineering controls to make the task safer. Other control measures may include administrative controls (such as work rotation or task scheduling) and personal protective equipment (such as back supports or gloves).
By following these steps‚ organizations can conduct thorough manual handling risk assessments that help them identify and control risks‚ ultimately creating a safer working environment for their employees.
Identify Hazardous Manual Handling Tasks
The first crucial step in conducting a manual handling risk assessment is to identify all tasks within the workplace that involve manual handling. This involves a systematic and thorough review of all work activities‚ focusing on tasks that require employees to lift‚ lower‚ push‚ pull‚ carry‚ or otherwise move‚ hold‚ or restrain any object or person. It’s essential to consider a broad range of tasks and not limit the assessment to only obvious lifting activities.
During this identification process‚ it’s helpful to consider the following factors⁚
- Frequency and Duration⁚ Tasks performed repeatedly or for extended periods are more likely to lead to musculoskeletal injuries.
- Load Characteristics⁚ The weight‚ size‚ shape‚ and stability of the load being handled can significantly influence the risk. Heavy‚ bulky‚ or awkwardly shaped objects pose greater risks.
- Task Complexity⁚ Tasks involving awkward postures‚ repetitive movements‚ or forceful exertion increase the risk of injury.
- Environmental Factors⁚ The surrounding environment‚ including lighting‚ space constraints‚ and potential obstacles‚ can influence the risk associated with manual handling tasks.
By meticulously identifying all hazardous manual handling tasks‚ organizations lay the foundation for a comprehensive risk assessment‚ ensuring that no task is overlooked and that appropriate control measures can be implemented to mitigate risks.
Assess Risk Factors
Once hazardous manual handling tasks have been identified‚ the next step is to assess the associated risk factors. This involves evaluating various aspects of the task‚ the load‚ the individual performing the task‚ and the environment in which the task is carried out. The aim is to understand the potential for injury and identify areas where improvements can be made.
Here are the key risk factors to consider⁚
- Load⁚ Assess the weight‚ size‚ shape‚ and stability of the load. Heavy‚ bulky‚ or awkwardly shaped loads increase the risk of injury. The position of the load‚ whether it is above or below shoulder height‚ can also impact risk.
- Individual⁚ Consider the physical capabilities of the individual performing the task‚ including their strength‚ fitness‚ and any pre-existing medical conditions. Factors like age‚ experience‚ and training should also be taken into account.
- Task⁚ Analyze the movements involved in the task‚ including lifting‚ lowering‚ pushing‚ pulling‚ carrying‚ and any awkward postures or repetitive motions. The frequency and duration of the task are also important considerations.
- Environment⁚ Evaluate the workplace environment‚ including factors like lighting‚ space constraints‚ floor surfaces‚ temperature‚ and the presence of any obstacles or hazards.
By systematically assessing these risk factors‚ organizations can gain a clearer picture of the potential for injury and identify specific areas where improvements can be implemented to reduce risks. This thorough evaluation is crucial for implementing effective control measures and ensuring a safer working environment.
Evaluate the Risk
After identifying hazardous manual handling tasks and assessing associated risk factors‚ the next crucial step is to evaluate the overall risk. This involves analyzing the likelihood of an injury occurring and the severity of the potential consequences. A systematic approach to risk evaluation helps prioritize actions and focus resources on the most significant hazards.
There are several methods for evaluating risk‚ including⁚
- Risk Matrix⁚ A simple but effective tool where risks are categorized based on their likelihood and severity. This allows for a quick visual assessment of the overall risk level.
- Quantitative Risk Assessment⁚ This involves assigning numerical values to the likelihood and severity of risks‚ allowing for a more precise assessment. This approach is often used for complex tasks or where there is a need for detailed analysis.
- Qualitative Risk Assessment⁚ This method relies on expert judgment and experience to evaluate risks based on subjective criteria. It can be useful when quantitative data is limited.
Regardless of the method used‚ the key objective is to determine the level of risk for each identified task. This involves considering the potential for injury‚ the severity of potential injuries‚ and the number of employees exposed to the risk. The results of the risk evaluation will then inform the development of appropriate control measures.
Control Measures
Once the risks associated with manual handling tasks are evaluated‚ the next step is to implement control measures to eliminate or minimize those risks. The goal is to create a safer working environment by reducing the likelihood of injuries and minimizing the severity of potential harm. Control measures should be prioritized based on the level of risk identified during the assessment process.
There are several types of control measures that can be implemented‚ including⁚
- Elimination⁚ This involves completely removing the hazardous manual handling task. This is the most effective control measure‚ but it may not always be feasible.
- Substitution⁚ This involves replacing the hazardous manual handling task with a safer alternative‚ such as using mechanical aids or automation.
- Engineering Controls⁚ These involve modifying the workplace or equipment to reduce the risk of injury. Examples include using ergonomic lifting devices‚ improving lighting‚ and providing accessible storage.
- Administrative Controls⁚ These involve changing work practices or procedures to reduce the risk of injury. Examples include limiting the weight of loads‚ providing training on proper lifting techniques‚ and scheduling work to reduce fatigue.
- Personal Protective Equipment (PPE)⁚ While PPE is not a primary control measure‚ it can be used as a last resort to protect employees from residual risks. Examples include back supports‚ gloves‚ and safety shoes.
Control measures should be implemented in a systematic and comprehensive manner to ensure the effectiveness of the risk assessment process. Regular monitoring and review are essential to ensure that control measures remain effective and are adapted to changing circumstances.
Examples of Manual Handling Risk Assessments
To better understand the process of conducting a manual handling risk assessment‚ let’s examine some real-world examples. These examples illustrate the different types of manual handling tasks that require assessment and the specific risk factors that need to be considered.
Example 1⁚ A warehouse worker lifting boxes from a pallet onto a shelf. This task involves lifting‚ carrying‚ and lowering heavy objects. The risk factors to consider include the weight of the boxes‚ the height of the shelves‚ the distance the worker needs to move the boxes‚ and the worker’s physical capabilities.
Example 2⁚ A nurse transferring a patient from a bed to a wheelchair. This task involves lifting‚ lowering‚ and supporting a person‚ and it requires careful consideration of the patient’s weight‚ mobility‚ and any existing medical conditions. The risk factors to consider include the patient’s weight‚ the height difference between the bed and the wheelchair‚ and the nurse’s lifting technique.
Example 3⁚ A construction worker carrying a load of bricks up a ladder. This task involves lifting‚ carrying‚ and climbing‚ and it presents a significant risk of falls and injuries. The risk factors to consider include the weight of the bricks‚ the height of the ladder‚ the stability of the ladder‚ and the worker’s physical fitness.
These examples highlight the diverse range of manual handling tasks that require risk assessment. By carefully analyzing the specific factors involved in each task‚ employers can identify potential hazards and implement appropriate control measures to protect workers from injury.
Resources and Templates
Numerous resources and templates are available to assist in conducting manual handling risk assessments. These resources provide valuable guidance‚ checklists‚ and forms to streamline the assessment process and ensure compliance with legal requirements.
One valuable resource is the Health and Safety Executive (HSE) website‚ which offers comprehensive guidance on manual handling risk assessments‚ including information on legal requirements‚ risk factors‚ control measures‚ and examples of assessment checklists. The HSE website also provides downloadable templates for conducting manual handling risk assessments‚ which can be customized to suit the specific needs of different workplaces.
Other organizations‚ such as the National Institute for Occupational Safety and Health (NIOSH)‚ also offer resources on manual handling risk assessment. NIOSH provides guidance on assessing risk factors‚ implementing control measures‚ and using tools like the NIOSH lifting equation to evaluate the risk of injury.
Additionally‚ various online platforms offer downloadable templates and forms for conducting manual handling risk assessments. These templates often include sections for identifying hazardous tasks‚ assessing risk factors‚ evaluating risks‚ and implementing control measures.
By utilizing these resources and templates‚ employers can ensure that their manual handling risk assessments are thorough‚ comprehensive‚ and compliant with legal requirements.